PDF FILE - CLICK HERE FOR PRINTABLE WORKSHEET | |
YouTube Video - Introduction to the Shaping Machine | |
The shaping machine is used to machine flat metal surfaces especially where a large amount of metal has to be removed. Other machines such as milling machines are much more expensive and are more suited to removing smaller amounts of metal, very accurately. The reciprocating motion of the mechanism inside the shaping machine can be seen in the diagram. As the disc rotates the top of the machine moves forwards and backwards, pushing a cutting tool. The cutting tool removes the metal from work which is carefully bolted down. | |
THE SHAPING MACHINE | |
CLICK HERE FOR MORE INFORMATION ON THE SHAPING MACHINE | |
The shaping machine is a simple and yet extremely effective machine. It is used to remove material, usually metals such as steel or aluminium, to produce a flat surface. However, it can also be used to manufacture gears such as rack and pinion systems and other complex shapes. Inside its shell/casing is a crank and slider mechanism that pushes the cutting tool forward and returns it to its original position. This motion is continuous. 1. Complete the diagram below by adding the missing parts that make up the crank and slider mechanism. | |
2. Why is the crank slider mechanism suitable for this type of machine especially the motion of the cutting tool? | |
3. Draw an alternative mechanism or combination of mechanisms that will produce the same forwards and backwards motion. Is your new mechanism an improvement on the crank and slider mechanism? | |
Draw a diagram of the shaping machine and explain how the quick return mechanism works. |
- Quick Return Mechanism In Slotting Machines
- Slotting Machine For Sale
- Slotting Attachment For Milling Machines
So what happens in quick return motion mechanism is, In the forward stroke, the Slider moves fast and removing the material from the workpiece. Whereas in the return stroke, the Slider moves faster than the forward stroke that means Quick return, it takes less time to return, called a return stroke. The shaper ram also can be driven in this manner, but many times a quick-return link mechanism is used. Most planers differ from shapers in that they approach more constant-velocity cutting speeds. Tools used in shaper and planer work are single point as used on a lathe, but are heavier in construction. Whitworth quick return mechanism is used in slotting machine,shapinfg machine and presses.
In this article we will discuss about:- 1. Introduction to Shaper 2. Shaper Size 3. Classification 4. Working 5. Hydraulic Shaper 6. Lubricating 7. Table Cross-Feed Mechanism 8. Quick Return Mechanism of Ram 9. Some Important Do’s and Do not’s.
Introduction to Shaper:
The shaper makes use of a single point tool that traverses the work and feeds over at the end of each stroke. It is used principally to machine flat or plane surfaces in horizontal, vertical and angular planes. The cutting tool is mounted on the shaper head to the ram.
The ram imparts a reciprocating motion to the tool which operates over the shaper table. It is generally not used as production machine; however, it is widely used in machine shops and tool rooms since it is easy to set up and operate.
ADVERTISEMENTS:
Also the cutters used are low in cost and are easily sharpened. A big advantage of it is that since the amount of metal removed at one time is relatively small in area, therefore, little pressure is imposed upon the work and the elaborate holding fixtures are not needed.
The work is usually held in a shaper vise, but sometimes it may be desirable to bolt it directly on to the table. The table is capable of being adjusted vertically by hand feed. Vertical cuts can be taken by feeding the tool with the shaper head slide. The shaper head can be set at an angle in order to take angular cuts.
The type of surfaces for which the shaper is best suited are shown in Fig. 14.1. It may be noted that shaper is very well suited for contour work which is done by coordinating the tool hand feed to a layout line, or by a duplicating attachment placed on the machine. Shaping operation is best suited for machining complex configurations like deep internal slots and difficult contours.
Although many shaper operations can more rapidly be performed by other form tools on milling machines but they require more costly tooling and setup. Therefore, the form tools would be economical only when the number of parts to be machined is large enough to justify a great initial investment.
While producing flat surfaces on shaper, it is observed that when tool comes into contact with the job, it digs into the job and, therefore the edges are generally not flat but slightly over curved. Same effect is observed at the end edges also. Due to its limited length of stroke, it is conveniently adapted to small job and best suited for surface composed of straight line elements and for batch production.
It can produce all types of surface finishes. The set up time and change over time are less as intricate fixtures and supporting devices are replaced by simple holding gadgets. It is also best suited for cutting keyways and splines on shafts. Thus, though the shaping process inherently slow, yet its use is quite popular because of short set-up time, inexpensive tooling and ease of operation.
In comparison to planer it occupies less space, consumes less power, costs less, occupies less floor area, is easier to operate and about three times quicker in action (as stroke length and moving mass are less). Its use is limited upto 750 mm stroke lengths as accuracy decreases for longer strokes due to overhang of ram.
ADVERTISEMENTS:
Cutting Parameters:
Average cutting speed in shaping/planning
V = NL (1 + Hm)/1000 m/min
where L = stroke length, in mm
N = number of complete strokes (both forward and return) per min
Hm = time for one return stroke / time for one forward stroke (less than unity).
Depth of cut (d) — It is the normal distance between the un-machined surface and machined surface.
Feed rate (f) — It is the intermittent movement of tool in a direction normal to the direction of cutting velocity and is expressed in mm/stroke.
ADVERTISEMENTS:
Uncut chip thickness = fa = f cos θs, where θs = side cutting edge angle of the tool.
Area of uncut chip = f.d.
Cutting edge engagement (6) = d/sin θs.
Chip cross-sectional area Ac = fd / sin θs.
Machining time = b/V,
Cutting power requirement = Fv x V/60 x 103
= specific cutting energy in N/mm2 x Av x V
Metal removal rate = fdV.
Shaper Size:
The size of a shaper is given by the maximum length of the stroke or rams movement. These are built in a wide range of sizes varying from 175 to 900 mm stroke. These are usually provided with power feeds ranging from 0.2 to 5 mm per stroke. The down feed is usually manual but power feed is also possible.
Shaper details like type of drive, type of speed reduction, power input, cutting to return stroke ratio, number and amount of feeds, total floor requirement, weight etc. are also mentioned to complete the specifications.
Classification of Shapers:
These are generally classified with respect to the plane of ram, i.e., vertical or horizontal.
The horizontal machines are further classified according to the action of the cutting stroke, i.e. push cut or draw cut. The push-cut type cuts in forward stroke and draw- cut type in backward stroke. The push-cut type shaper is most popular one and unless otherwise specified, the term shaper refers to this type. In the use of draw-out type shaper, the ram is very heavy and is used for heavier cuts with less strain in the work-table.
A further classification of the horizontal shaper is as plain or universal. In universal shaper, angular cutting is also possible as the table can be swivelled around the horizontal axis. Further depending upon the accuracy and attachments, these could also be classified as production or tool-room type.
The vertical shaper is very much the same as slotter. In it, the cutting thrust acts directly on the table bed and also there is no possibility of deflection of table. Simple holding fixtures are needed as the cut tends to force the work onto the table. For accurate positioning of work, the table is provided with movements in three directions.
According to the type of drive, the shapers can be classified as crank driven shaper, geared shaper or hydraulic shaper.
Working on Shaper:
For accurate working and obtaining the best results on shaper the following settings must be ensured and tested properly before proceeding to work on shaper.
(i) Work table on work seat in the vise for parallelism with the movement of ram.
(ii) Squareness of vise jaws.
(iii) For vertical facing, the tool movement should be exactly perpendicular to the table.
(iv) Proper setting of job for parallelism.
For this purpose, use of dial indicator, try-square and feeler gauges could be made.
Generally the surface cutting speed is known for the cutting tool material and the metal to be machined. From it, the approximate number of strokes/minute to be used can be calculated. If L is the length of stroke in mm and N is the number of strokes per minute, then length cut in one minute = N x L / 1000 metres.
But actual cutting time for machining is only in forward stroke. Therefore, out of total time (α + β), α is for actual cutting and β for idle stroke.
Cutting Speed:
= ((N x L) / 1000) + (α / (α + β)) = [(N x L) / 1000] ((α + β) / α) m/minute.

Whenever possible the strokes/mt as calculated by above formula should be used; however, it is sometimes necessary to reduce this speed because of the nature of the operation being performed or the rigidity of the setup of the workpiece.
As regards feed and depth of cut, as a general rule, for rough cuts, as much feed and depth as possible, should be used leaving about 0.1 to 0.7 mm on the workpiece for finishing cut. In selection of feed rate and depth of cut the factors like h.p. of machine, length of stroke, set up of workpiece, its rigidity, amount of stock to be removed, finish required should be given due consideration. The feed to be used for finish cutting depends upon the type of cutting, tool selected for this purpose.
The normal values of cutting speeds and feeds are given below in the table. For roughing, feed rate should be about 1/10th the depth of cut (for deep cuts of the order of 1 cm), and 1/3rd to 1/2 the depth of cut (for shallow roughing cut of the order of 2.5 mm). For finishing, feed rate is dependent on the shape of the tool which generally is square on the nose and is fed 3/4 of tool width on each stroke.
The finishing speed is generally faster than that used for deep roughing cuts and slightly slower than that for shallow roughing cuts. In any case speed is much less than that for turning. Depth of cut depends upon microstructure and hardness of work-piece, amount of metal to be removed, power available, rigidity of workpiece etc.
However it should not be less than 0.4 mm as shallow cuts do not allow sufficient tool bite, resulting in chatter and glazing of workpiece surface. It is common practice in shaping to use maximum feeds at slow speeds for roughing cuts and higher speeds and lower feeds for finish machining.
Very low feed rates do not allow sufficient tool bite and result in chatter. Similarly depth of cut (less than 0.4 mm) results in chatter and glazing of the workpiece surface. Depth of cut in shaping is influenced by the microstructure and hardness of the workpiece, amount of metal to be removed, workpiece size, workpiece configuration, rigidity of the set up and the available power.
Carbide tools must have negative back and side rakes to provide maximum support to the cutting edge. H.S.S. tools must have high vanadium which improves impact resistance and less cobalt which introduces brittleness.
Hydraulic Shaper:
Hydraulic mechanisms are becoming increasingly popular because of the followingadvantages:
(i) Greater flexibility of speed.
(ii) Smoother operation.
(iii) Ability to slip in case of overload.
(iv) Ability to withstand against an obstruction without damage to the tool or the machine.
(v) Possibility of changing speed and feed during operation.
(vi) Velocity diagram of hydraulically operated shaper shows a very nearly constant velocity as compared with the crank shaper as shown in Fig. 14.7.
A simple mechanism of hydraulic drive is shown in Fig. 14.8. A constant speed motor drives a hydraulic pump which delivers oil at a constant pressure to the line. A regulating valve actuated by the machine and timed to the stroke, admits oil under pressure to each end of piston alternately at the same time allowing oil from the opposite end of the piston to return to the reservoir.
As the piston moves, it carries the ram and the cutting tool along with it. Since it is a constant pressure system, therefore, the tool moves at slightly different velocities under varying load conditions.
One end of the piston is having large area and other end has less area due to piston rod. Therefore, in one stroke it moves at low speed and in opposite stroke it moves at high speed. The velocity can also be controlled by a simple handle, which regulates the quantity of oil.
Some hydraulic systems are very complicated, and incorporate controls for changing the velocity, cross-feed etc. and have many other refinements.
Lubricating the Shaper:
The trouble free operation and the life of any machine tool to a very great extent depends on the proper lubrication and strictly following the daily, weekly, and monthly oiling schedule recommended by the manufacturer.
Daily Lubrication:
(i) Clean the surface of the table and the sliding surfaces of the rail.
(ii) Clean and oil the sliding surfaces of the tool head, the sliding surfaces for the vise.
(iii) Oil the feed screw bearing, feed screw, clapper pin, etc.
Weekly Lubrication:
(i) Oil the ram-adjusting screw through the opening in the ram, the speed-change-lever bearings, the crank clutch.
(ii) Fill the oil holes at rear of the ram and near the ram adjusting shaft.
Monthly Lubrication:
Remove the plug and add oil to the feed box.
Table Cross-Feed Mechanism:
The idea of table feed mechanism is that when the ram is moving back, i.e. in idle stroke the table should be cross-fed so that next time the tool takes cut in different line. It may be done either manually or automatically.
Also an arrangement is provided to vary the amount of cross-feed per stroke depending upon the finish desired. A gear E is placed concentric to bull gear G and the gear E is in mesh with a gear F having a slot in it as shown in Fig. 14.6.
A slider B can move in this slot and a connecting rod is connected to this slider at one end and to a pawn arm at the other end. By changing the position of B the radius R can be changed and thereby the amount of swinging of pawn arm can be adjusted.
The ratchet wheel is rotated a little with the help of swinging of the pawn arm and the cross-feed screw is also connected with the ratchet wheel. For automatic feed, the pawn is connected in the ratchet wheel, otherwise it is pulled outside. The amount of feed per stroke is changed by changing radius R.
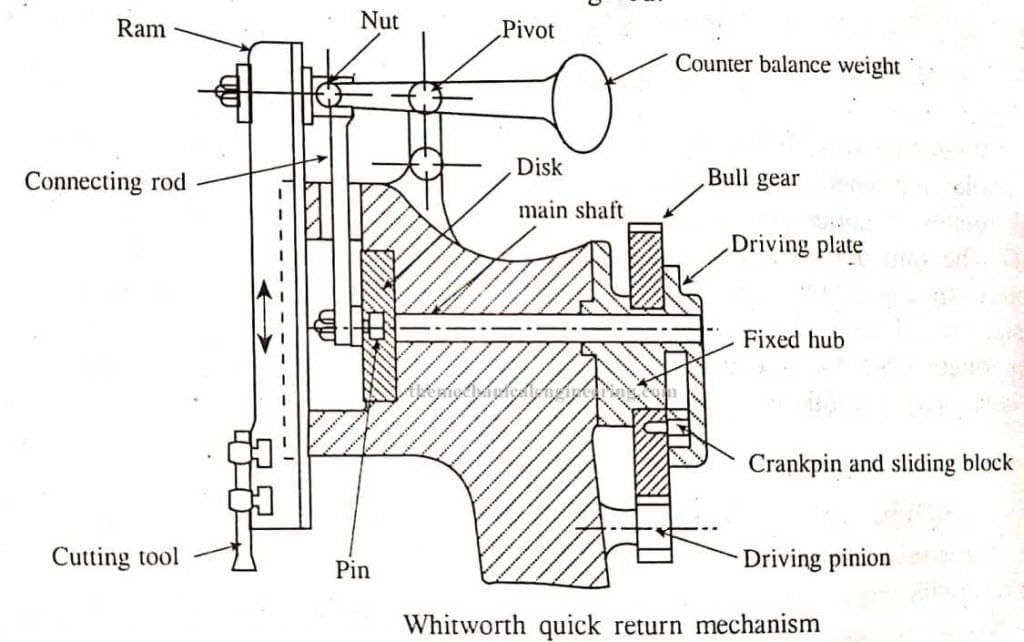
Quick Return Mechanism of Ram:
A shaper does the cutting operation only in the forward stroke, and backward stroke is idle and, therefore, wastage. In order to minimise this wastage, the return stroke should be completed as quickly as possible. This is achieved by employing a crank-slotter mechanism explained below.
In Fig. 14.4, AB represents the crank rotating about centre A. B constitutes a slotter and has both rotating and sliding motions. Link CO is fixed at point O and car rotate about it. It has a slot through which a block B can slide. Thus when the crank rotates about its centre A, link CO oscillates about its centre O between its ultimate positions OC1 and OC2. Oscillating motion of CO makes the ram to reciprocate through link CD.
It may be noted that the ram stroke length is proportional to the crank length AB. If the distance between A and B is more, stroke will be longer and vice versa.
In Fig. 14.4, the forward stroke is constituted from the crank position AB1 to AB2 during its anti-clockwise movement, whereas the return stroke is from AB2 to AB1. Thus the ratio of forward to the return stroke is equal to ratio of angle α and β. The usual ratio of forward and return stroke is of the order of 3 : 2.
Fig. 14.5 shows complete details of driving mechanism of a typical shaper. Drive from the motor is coupled to gear F which is in mesh with the bull gear G, whose centre is at A. There is a slider S which slides in the slot of rocker arm CE and a pin B passes through the slider S and is fixed on the bull gear. Thus distance AB here constitutes the crank.
When gear F drives the bull gear G, the block S also rotates about the bull gear centre A and side by side slides through the slot of the link CE, resulting in the oscillation of rocker arm CE. The shaper arm is also connected to the rocker arm by a connecting link CD.
The shaper arm is a hollow structure in which a screw M is fitted which can be rotated by rotating bevel gear drive Q. From the top the arm is slitted also.
The connecting rod is connected to arm through a block P threaded on screw M. The block P can be fixed in position by a nut L. Thus whenever the relative position of ram is to be changed the nut L is loosened and the screw M is revolved by bevel gears. Then the nut is tightened by operating the lever K and thus the link CE gets a sound connection with the ram.
The stroke length is varied by varying the distance AB. For this a simple arrangement as shown in Fig. 14.5 is provided, in which screw R is fitted in the slider S and can be rotated by bevel gears H and J, the drive to which is brought outside the shaper body. Thus by rotating screw R, distance AB can be changed and hence the stroke length of the shaper.
It may be seen from Fig. 14.5 that a connecting link connects the rocker arm EC to the link block P. The position of this link block can be changed by turning the screw M which is threaded through the upper portion of this block.
Since the link block P is held in a stationary position by the connecting link and the rocker arm when the bull gear is not turning, it is the ram which moves forward and back when the screw M inside of the ram is turned.
In this manner the position of the ram can be adjusted so that the cutting tool strokes back and forth in the right location on the work-piece. When the shaper is cutting, the link block P must be clamped firmly to the ram. The ram adjusting shaft rotates the screw M through bevel gears Q.
Some Important Do’s and Do not’s in the Use of Shapers:
a. Always keep the machine clean and well oiled.
b. Use the proper wrench and handle, and when not in use, keep them at proper specified place.
c. Never use a vise jaw that has been dented, scored, or is out of true. Always use brass or copper or card board to protect the jaws when clamping the rough surfaces of the bar stock/castings/forgings.
d. Never run the ram back into the column with the slide rest set at an angle.
Quick Return Mechanism In Slotting Machines
e. Parallels should be kept clean, free from burrs, straight, parallel, and square. Never hammer a rough piece down on a parallel.
f. No chips should be left on the seating surfaces, or the clamping surfaces of the vise, parallels, and work.
g. Select the proper tool, grind it carefully, and oilstone it.
h. Use a Babbitt hammer or ball to seat the work. Never use a wrench for this purpose.
i. Never hammer the work with the Babbitt, but tap it just hard enough to seat. Never tighten the vise after work is seated, otherwise work may lift slightly.
j. Never pinch a thin piece of work too tight otherwise it may be out or true or buckle when pressure is released.
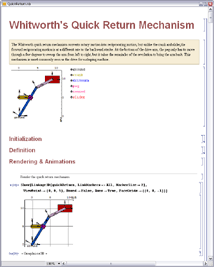
k. Before placing a vise on table, ensure that top of table and bottom of vise place are clean and free from burrs.
l. While setting up irregular work, it should be ensured that head and bottom of the ram will clear the work during the whole length of stroke and whole width of the cut.
m. Always ensure that the tool block seats properly and works freely.
n. Never hammer the side of the apron to swivel it. If the edge of the seating surfaces of the apron is dented and burred, it will cause the tool block to bind in the box.
o. Adjust the stroke of the shaper as the length of the work to be machined.
p. Before starting a shaper make sure that the work, vise, tool, and ram are securely fastened.
q. Check that the tool and tool holder will clear the work and also clear the column on the return stroke.
r. Always prevent chips from flying by using a wire screen and stand on one side of the cutting stroke to prevent injury from flying chips.
s. Always stand parallel to the cutting stroke and not in front of it.
t. Never attempt to remove chips or reach across the table while the ram is in motion.
Slotting Machine For Sale
u. Never attempt to adjust a machine while it is in motion.
v. Swing the apron so that the cutting tool does not rub on the return stroke.
w. Keep the area around a machine neat and tidy. Clean oil and grease from the floor immediately to prevent dangerous falls.
Slotting Attachment For Milling Machines
x. Offset the chapper box when machining a vertical surface.